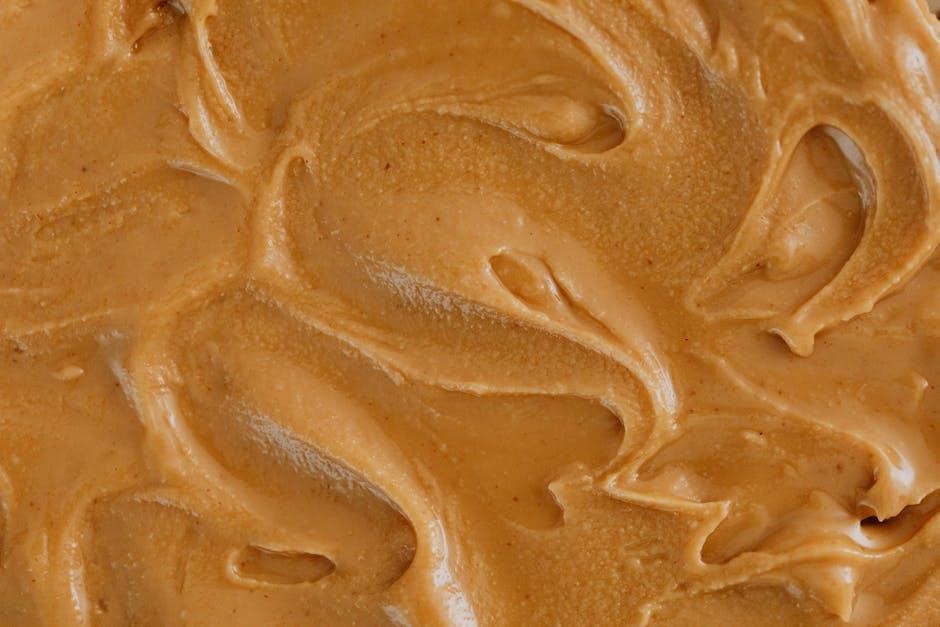
md-83 acme screw and nut pdf
The MD-83 Acme screw and nut assembly is a critical component of the horizontal stabilizer, enabling precise pitch control during flight. It consists of an Acme screw, nut, torque tube, and associated gearboxes and motors. Proper lubrication and maintenance are essential to prevent wear and ensure reliable operation, as highlighted by incidents like Alaska Airlines Flight 261. The assembly’s performance directly impacts flight safety and stability, making it a focal point for regular inspection and adherence to manufacturer guidelines.
1.1 Overview of the Jackscrew Assembly
The jackscrew assembly in the MD-83 aircraft is a vital component of the horizontal stabilizer control system. It comprises an Acme screw, an Acme nut, a torque tube, two gearboxes, and associated trim motors. This assembly converts rotary motion from the motors into linear motion, enabling precise pitch control during flight. Proper lubrication and maintenance of the jackscrew assembly are critical to prevent wear and ensure reliable operation, as highlighted by incidents such as Alaska Airlines Flight 261, where insufficient maintenance led to catastrophic failure.
1.2 Importance of the Acme Screw and Nut in Flight Controls
The Acme screw and nut are essential for the MD-83’s flight controls, enabling precise and reliable pitch trim adjustments. Their role in converting motor-driven rotary motion to linear movement is critical for stabilizer positioning. Failure due to wear or insufficient lubrication, as seen in historical incidents, underscores their importance in maintaining flight safety. Proper maintenance ensures consistent performance, preventing potential control issues that could compromise aircraft stability and safety during operation.
Maintenance Procedures for the Acme Screw and Nut
Regular lubrication, detailed inspections, and torque checks are essential for maintaining the Acme screw and nut assembly’s functionality and safety in the MD-83 aircraft.
2.1 Lubrication Requirements and Schedule
Regular lubrication of the Acme screw and nut assembly is critical to prevent wear and ensure smooth operation. The Boeing AMM recommends applying grease through the zerk fitting on the stationary nut every 600 flight hours. Proper lubrication prevents excessive thread wear and potential failure, as highlighted by the NTSB findings in the Alaska Airlines Flight 261 incident. Over-lubrication should be avoided to prevent grease degradation and contamination. Adhering to the schedule ensures optimal performance and safety of the flight control system.
2.2 Inspection and Wear Detection Methods
Inspecting the Acme screw and nut assembly involves visual checks for wear, measuring screw thread dimensions, and verifying proper alignment. Technicians use specialized tools to detect excessive wear or damage. The FAA recommends inspecting the assembly every 600 flight hours, aligning with Boeing’s AMM guidelines. Signs of wear include thread deformation, fretting corrosion, or abnormal play. Early detection prevents catastrophic failure, ensuring flight control reliability and safety.
2.3 Torque Specifications for Nut Tightening
Tightening the Acme nut requires adherence to precise torque specifications to avoid over- or under-tightening, which can lead to premature wear or failure. According to Boeing’s AMM, the recommended torque for the Acme nut is 120-140 ft-lbs. Proper torque ensures the assembly operates smoothly and maintains structural integrity. Technicians must use calibrated tools to apply the correct torque, following the sequence outlined in the maintenance manual to ensure even loading and prevent component damage.
Historical Context and Safety Incidents
The MD-83 Acme screw and nut assembly has been linked to significant safety incidents, notably Alaska Airlines Flight 261, where insufficient lubrication caused catastrophic failure. Historical data highlights the importance of adherence to maintenance protocols to prevent such tragedies, underscoring the critical role of proper lubrication in ensuring component longevity and flight safety.
3.1 The Alaska Airlines Flight 261 Case Study
On January 31, 2000, Alaska Airlines Flight 261, an MD-83, crashed due to failure of the horizontal stabilizer’s jackscrew assembly. The NTSB investigation revealed insufficient lubrication of the Acme nut, causing excessive wear and eventual failure. This tragedy highlighted critical maintenance oversights and led to revised FAA and manufacturer guidelines, emphasizing proper lubrication schedules and inspection practices to prevent similar incidents. The crash remains a pivotal lesson in the importance of adhering to maintenance protocols for flight control systems.
3.2 NTSB Findings on Jackscrew Assembly Failure
The NTSB determined that the primary cause of the MD-83 jackscrew assembly failure in Alaska Airlines Flight 261 was insufficient lubrication of the Acme nut. This led to excessive wear on the nut threads, causing the assembly to fail during flight. The investigation highlighted inadequate maintenance practices and insufficient oversight of lubrication schedules. The NTSB recommended stricter adherence to manufacturer guidelines and enhanced inspection protocols to prevent similar failures in the future, emphasizing the critical role of proper maintenance in ensuring flight safety.
Regulatory and Manufacturer Guidelines
FAA and Boeing guidelines emphasize strict maintenance protocols for the MD-83 Acme screw and nut, including lubrication schedules and torque specifications to ensure optimal performance and safety.
4.1 FAA Recommendations for Maintenance
The FAA mandates rigorous maintenance protocols for the MD-83 Acme screw and nut assembly, emphasizing periodic lubrication and inspection. Guidelines include applying grease to the Acme nut until it exits, ensuring proper torque specifications, and adhering to scheduled inspection intervals. The FAA also recommends following task cards for end play checks to prevent excessive wear. Compliance with these directives is critical to avoid failures, as highlighted by incidents like Alaska Airlines Flight 261, where insufficient lubrication led to catastrophic consequences.
4.2 Boeing’s AMM Specifications for MD-83
Boeing’s Aircraft Maintenance Manual (AMM) for the MD-83 provides detailed specifications for the Acme screw and nut assembly. It outlines lubrication procedures, torque values, and inspection intervals to ensure optimal performance. The manual specifies applying grease to the Acme nut until it exits, verifying torque specifications during assembly, and conducting periodic end play checks using task cards. Adherence to these guidelines is crucial for maintaining system reliability and preventing failures, aligning with broader maintenance practices for the aircraft’s flight control systems.
Technical Specifications of the Acme Screw and Nut
The Acme screw and nut assembly is precision-engineered with high-strength alloys, featuring a 1-inch major thread diameter and 0.5-inch pitch. The nut’s internal dimensions match the screw’s external threads, ensuring smooth engagement. Torque capacity is optimized for the MD-83’s flight control loads, with strict tolerance standards to maintain system integrity and performance.
5.1 Design and Material Composition
The MD-83 Acme screw and nut assembly is crafted from high-strength, corrosion-resistant alloys to endure extreme flight conditions. The screw features a precision-machined Acme thread, while the nut is designed for optimal thread engagement and load distribution. Both components are treated with wear-resistant coatings to minimize friction and extend service life. The assembly includes a torque tube and gearbox, ensuring precise control of the horizontal stabilizer. Materials are selected for durability, with the screw typically made from hardened steel and the nut from bronze or similar high-strength alloys.
5.2 Dimensional Tolerances and Compatibility
The MD-83 Acme screw and nut assembly must meet stringent dimensional tolerances to ensure proper fitment and functionality. The screw and nut are precision-manufactured to exacting standards, with thread dimensions carefully controlled to maintain compatibility. The assembly is designed to work seamlessly with the horizontal stabilizer and associated flight control systems. Dimensional accuracy ensures smooth operation, while compatibility with adjacent components prevents misalignment or binding. These tolerances are critical to maintaining the structural integrity and performance of the aircraft’s flight control systems.
Troubleshooting Common Issues
Identifying symptoms like excessive wear or misalignment is crucial. Diagnostic tools and techniques help detect issues early, ensuring timely resolution and preventing system failures. Regular inspections are key.
6.1 Symptoms of Excessive Wear or Misalignment
Symptoms include abnormal noise during operation, increased backlash between the Acme screw and nut, and visible wear patterns. Misalignment may cause uneven stress distribution, leading to premature component failure. Regular inspections can identify these issues early, preventing catastrophic malfunctions. Addressing these symptoms promptly ensures the integrity and reliability of the flight control system, maintaining aircraft safety and performance. Early detection is critical to avoid costly repairs and potential safety hazards.
6.2 Diagnostic Tools and Techniques
Diagnostic tools include visual inspection for wear, torque wrenches to check nut tightness, and flaw detectors for internal damage. End play measurements and lubrication analysis are also critical. Maintenance manuals provide detailed procedures for these checks, ensuring accurate assessments. Regular use of these tools helps identify issues early, preventing system failure. Technicians rely on these methods to maintain component integrity and ensure safe operation. Proper diagnostic techniques are essential for extending service life and reliability.
Scheduled Maintenance Tasks
Periodic lubrication, end play checks every 6 months, and torque verification ensure optimal performance. Worn components are replaced based on manufacturer guidelines to prevent failure.
7.1 Periodic Inspection Intervals
Inspections of the Acme screw and nut assembly are scheduled every 6 months, focusing on lubrication condition, wear, and end play. Visual checks ensure no thread damage or excessive wear, while torque specs are verified. These intervals align with FAA and Boeing recommendations, as highlighted by the Alaska Airlines incident, emphasizing the importance of regular maintenance to prevent failure and ensure flight safety. Adherence to these schedules is critical for reliability and compliance with manufacturer guidelines.
7.2 Replacement Criteria for Worn Components
Replacement of the Acme screw and nut components is mandatory when wear exceeds 0.015 inches or threads show visible damage. If lubrication is insufficient or corrosion is detected, replacement is also required. The NTSB recommends replacing components exhibiting excessive wear to prevent catastrophic failure, as seen in historical incidents. Adhering to these criteria ensures safety and optimal performance, aligning with FAA and Boeing guidelines for the MD-83 assembly maintenance.
Case Studies and Real-World Applications
The Alaska Airlines Flight 261 incident highlighted the critical importance of proper Acme screw and nut maintenance, underscoring the necessity of adhering to established procedures to ensure safety.
8.1 Lessons Learned from Maintenance Practices
The Alaska Airlines Flight 261 incident underscored the importance of proper lubrication and inspection of the Acme screw and nut assembly. Regular maintenance practices, such as applying grease to the Acme nut and conducting end-play checks, are critical to preventing excessive wear. The NTSB findings highlighted that neglecting these procedures can lead to catastrophic failures. Adhering to FAA and Boeing guidelines ensures the integrity of flight control systems, ultimately safeguarding aircraft safety and performance.
8.2 Industry Best Practices for Screw and Nut Maintenance
Industry best practices emphasize adhering to FAA and Boeing guidelines for maintaining the Acme screw and nut assembly. Regular lubrication with approved grease, following specified schedules, is crucial. Torque specifications must be strictly followed during nut tightening to prevent damage. Visual inspections and wear checks should be documented, with worn components replaced promptly. These practices, highlighted by incidents like Alaska Airlines Flight 261, ensure optimal performance and safety, underscoring the importance of meticulous maintenance protocols.
Future Developments and Improvements
Future developments focus on advancing materials science, predictive maintenance technologies, and integrating AI-driven monitoring systems to enhance the Acme screw and nut assembly’s reliability and lifespan, reducing maintenance challenges.
9.1 Advances in Materials and Lubrication
Research focuses on developing advanced materials like high-strength alloys and ceramic coatings to enhance durability and resistance to wear. Improved lubricants with better thermal stability and wear resistance are being tested to reduce maintenance needs. These innovations aim to extend component lifespan and improve reliability, addressing historical issues like those in Alaska Airlines Flight 261. New materials and lubrication techniques will help minimize downtime and ensure safer flight operations.
9.2 Emerging Technologies for Predictive Maintenance
Emerging technologies such as IoT sensors and machine learning algorithms are revolutionizing predictive maintenance for the MD-83 Acme screw and nut assembly. These tools enable real-time monitoring of wear patterns and lubrication levels, allowing for early detection of potential failures. Advanced analytics can predict when maintenance is required, reducing unscheduled downtime. Such innovations enhance safety by preventing incidents like Alaska Airlines Flight 261 and optimize maintenance schedules, ensuring optimal performance and longevity of critical components.