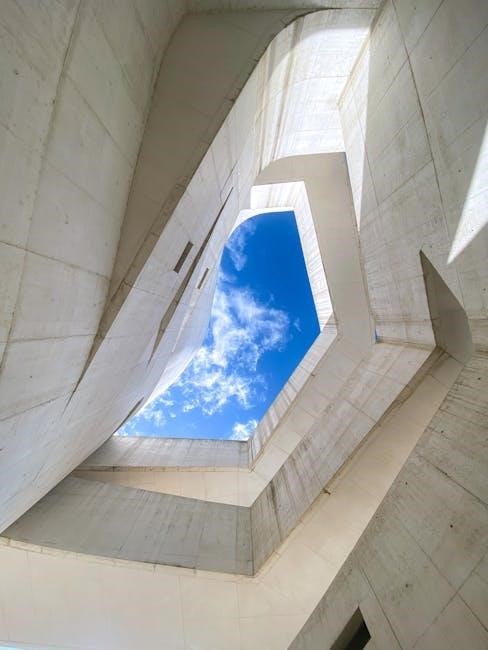
as rs pdf
An Automated Storage and Retrieval System (AS/RS) is a computer-controlled solution for efficiently handling, storing, and retrieving materials in industrial and distribution environments, optimizing space and accuracy.
Overview of Automated Storage and Retrieval Systems
An Automated Storage and Retrieval System (AS/RS) is a cornerstone of modern material handling, designed to optimize the storage, retrieval, and management of goods in industrial and distribution environments. These systems integrate advanced technologies, including computer controls, automated retrieval machines, and storage racks, to ensure efficient and accurate inventory management. AS/RS solutions are widely used in manufacturing, distribution centers, and warehouses to streamline operations, reduce labor costs, and enhance productivity. By automating key processes, AS/RS minimizes errors and maximizes space utilization, making it a critical component of lean and agile supply chain strategies. The system’s ability to handle a variety of load sizes, from unit-load to mini-load configurations, ensures versatility across industries. With real-time tracking and reporting capabilities, AS/RS provides unparalleled visibility into inventory levels, enabling businesses to respond swiftly to changing demands.
Definition and Scope of AS/RS
An Automated Storage and Retrieval System (AS/RS) is a material handling solution integrating equipment and controls for automated storage, retrieval, and inventory management with high accuracy.
Understanding the Basics of AS/RS Technology
AS/RS technology revolves around computer-controlled systems that automate the storage and retrieval of materials. At its core, it combines hardware, such as storage racks, conveyor systems, and retrieval machines, with software that manages inventory and directs operations. This integration ensures efficient, accurate, and rapid handling of goods, minimizing human intervention. Key components include automated retrieval machines that navigate aisles to store or fetch items, inventory management software for tracking stock levels, and conveyors for transporting goods within the system. AS/RS systems are designed to maximize space utilization and reduce operational costs while maintaining high throughput and precision. They are widely adopted in industries like manufacturing, distribution, and logistics to streamline warehouse operations and enhance overall efficiency.
Types of AS/RS
AS/RS systems are categorized into unit-load for handling large items like pallets and mini-load for smaller goods. Other types include vehicle, flow-rack, and push-back systems, each serving specific operational needs.
Unit-Load AS/RS
Unit-Load AS/RS systems are designed to handle large items, such as pallets or heavy containers, making them ideal for manufacturing and distribution centers. These systems use automated retrieval machines to store and retrieve loads efficiently. They are typically used for high-density storage, minimizing warehouse space while maximizing capacity. The systems are computer-controlled, ensuring precise and rapid access to stored items. Unit-Load AS/RS is particularly beneficial for industries requiring high throughput and accuracy, such as automotive and food processing. By integrating with inventory management systems, they enhance order fulfillment and reduce operational costs. This type of AS/RS is known for its reliability and scalability, adapting to the specific needs of large-scale operations. Its ability to optimize space and improve efficiency makes it a cornerstone in modern material handling solutions.
Mini-Load AS/RS
Mini-Load AS/RS systems are designed for handling smaller items, such as cartons, bins, or individual products, making them ideal for industries requiring precise and efficient inventory management. These systems use automated retrieval machines equipped with telescopic forks or other specialized tools to access and move items stored in high-density racks. Mini-Load AS/RS is particularly suited for applications where high throughput and rapid order fulfillment are critical, such as in e-commerce, pharmaceuticals, and electronics manufacturing. By optimizing storage space and reducing retrieval times, Mini-Load systems enhance operational efficiency and accuracy. They are also scalable, allowing businesses to adapt to changing demands. The ability to integrate with inventory management software ensures real-time tracking and seamless order processing. Mini-Load AS/RS is a valuable solution for organizations needing to manage smaller, high-value items with maximum precision and speed.
Historical Development of AS/RS
The concept of AS/RS emerged in the late 1970s, evolving from manual storage systems to automated solutions. Over time, advancements in technology and material handling needs drove its development.
Evolution from Manual to Automated Systems
The transition from manual to automated storage and retrieval systems (AS/RS) marked a significant leap in warehouse efficiency. Historically, manual systems relied heavily on human labor, leading to inefficiencies, errors, and safety concerns. The introduction of automation in the late 20th century revolutionized material handling by integrating computer-controlled technologies. Early AS/RS solutions focused on unit-load systems, managing large pallets of goods. Over time, advancements in robotics, software, and sensor technologies enabled the development of more sophisticated systems, such as mini-load and shuttle-based AS/RS. These systems offered greater flexibility, precision, and scalability, catering to diverse industrial needs. The evolution from manual to automated systems has not only enhanced operational speed and accuracy but also reduced labor costs and optimized storage space, making AS/RS indispensable in modern logistics and manufacturing environments. This shift underscores the industry’s continuous pursuit of innovation to meet growing demand and complexity in global supply chains.
Key Components of AS/RS
Storage racks, automated retrieval machines, and conveyors form the core components of AS/RS, enabling efficient storage, retrieval, and transportation of materials within industrial facilities.
Storage Racks and Automated Retrieval Machines
Storage racks are a fundamental component of AS/RS, designed to maximize vertical and horizontal space for high-density storage. These racks are typically tall and narrow, allowing for efficient organization of pallets or containers. Automated retrieval machines, such as cranes or shuttles, are equipped with telescopic forks or other mechanisms to handle loads. These machines travel along aisles between the racks, guided by computer systems to ensure precise storage and retrieval operations. The integration of storage racks and retrieval machines enables seamless inventory management, minimizing manual intervention and enhancing operational accuracy. Together, these components form the backbone of AS/RS, ensuring efficient material handling and optimal use of warehouse space.
Benefits of Implementing AS/RS
AS/RS enhances efficiency, optimizes space, and reduces operational costs by automating storage and retrieval processes, ensuring accurate inventory management and minimizing manual labor requirements.
Efficiency, Space Optimization, and Cost Reduction
Automated Storage and Retrieval Systems (AS/RS) significantly enhance operational efficiency by streamlining storage and retrieval processes, reducing manual labor, and minimizing errors. These systems optimize space by utilizing vertical storage solutions, such as tall racks, enabling high-density storage in smaller footprints. Additionally, AS/RS reduces costs through energy efficiency, lower labor expenses, and extended system longevity. With precise inventory tracking and real-time reporting, businesses achieve higher throughput and faster order fulfillment. The integration of advanced technologies ensures scalability, adapting to evolving operational demands while maximizing Return on Investment (ROI).
- High-density storage reduces warehouse space requirements.
- Automated operations minimize human error and improve accuracy.
- Lower operational and maintenance costs enhance profitability.